Innovation often begins the moment you realize that your company can create the very thing it depends on to succeed. And more importantly, that you can provide it, with the same standard of care, to others. When Miura was established in Japan in 1927, the company relied on steam to manufacture its rice threshing machines. Soon it was clear that more efficient, reliable steam would be needed in other areas. So, in 1959, Miura switched gears. They designed and began production of compact boilers and set off to change the future of boiler rooms worldwide.Mark Utzinger, Executive VP, has been with the company for 33 years and seen the growth and success firsthand. “The founder of the company, Tamotsu Miura, had dreams of eventually expanding to the U.S.” That kind of ambition falls in line with the company’s philosophy, called ‘kaizen”. Kaizen is a Japanese word that refers to constantly improving by using a gradual and methodical process. Mark explains that throughout the company, staff have their own instances of kaizen, and they use them to strategically improve every aspect of the business. “It’s something we all strive for daily and really live by. It can just be a small change that improves efficiency or quality or life. But it’s always a step toward something better.”
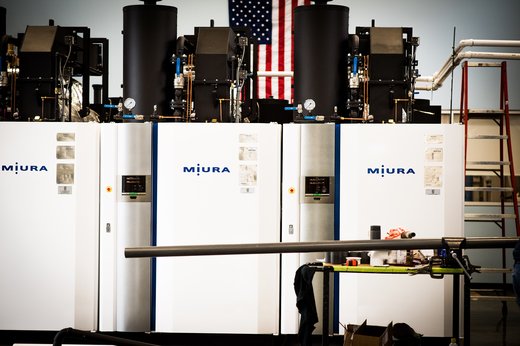
In 1987, Miura opened their first North American facility in Ontario. By 2008, the expanding economy was driving higher demand for Miura’s energy-efficient boilers. They were creating systems that were being used across countless industries from hospitals, event centers, universities, laundry companies, even breweries. “Boilers may not be something everyone thinks of often,” says Mark, “but they really are the heart of a building.” Later that same year, the economy took a drastic turn. “When the bubble burst, it caused a lot of changes in business practices. There was much more thought given to ways to save money and use less energy,” Mark Utzinger explains. “Our boilers are compact in design, which gives means more capacity in a smaller space. They are 20% more efficient than the alternatives, which saves fuel. And it’s an integrated system, meaning we also make the tanks, chemicals, everything that you need, which adds a lot of value.”
By 2009, the Canada location had reached full production capacity. Miura, as Mark puts it, “couldn’t make boilers fast enough.” Since much of the product was being shipped to the Southeast U.S., they knew it was finally time to make that initial dream into a reality. “There was definitely a time crunch. We needed the new facility to be operational very quickly for us to meet demand. With so little time to work with, we really felt lucky when we found that opportunity in Georgia.”
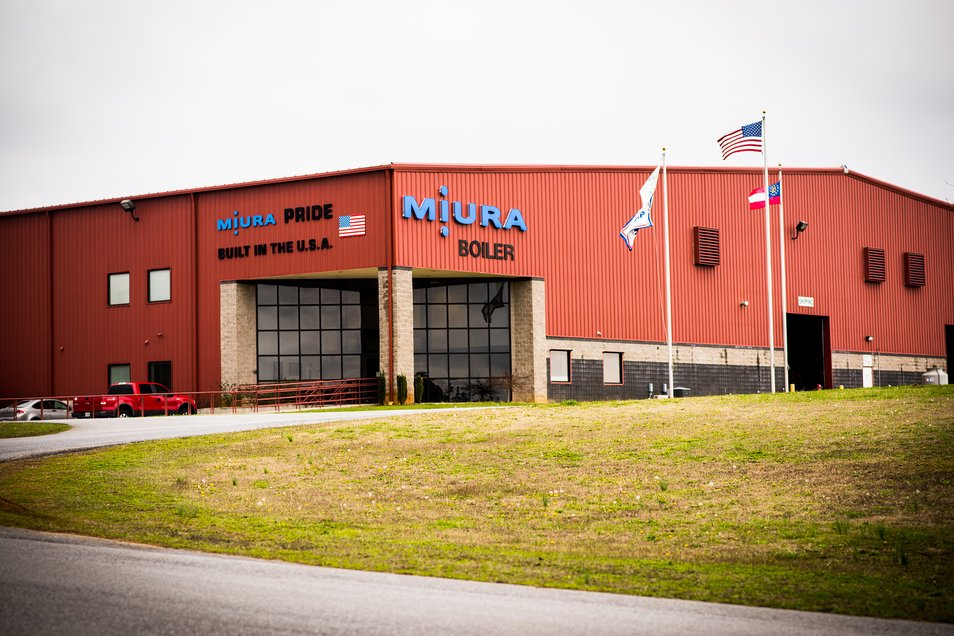
Scouting a new location is no small endeavor, even when time isn’t an obstacle. It was crucial that Miura work with state and local partners who could accommodate the short timeline. They knew they needed to be in a place with easy international access for both their people and cargo. “Workforce was also a factor,” recalls Mark. “Georgia’s QuickStart program was on board to help with training, so we were looking for a place where those potential employees were living.”
An available, 100,000-square foot spec building in Polk County was the break Miura needed. The space fit the factory needs, and the community was perfect for their people. The coastal ports would provide easy access for global shipping, and the busiest airport in the world would get executives and partners back and forth as needed. “Both the state of Georgia and Polk County were very helpful in getting us settled,” Mark recalls. “It was a win-win. Our location makes us extremely accessible to anywhere, and we really love being a part of this community.”
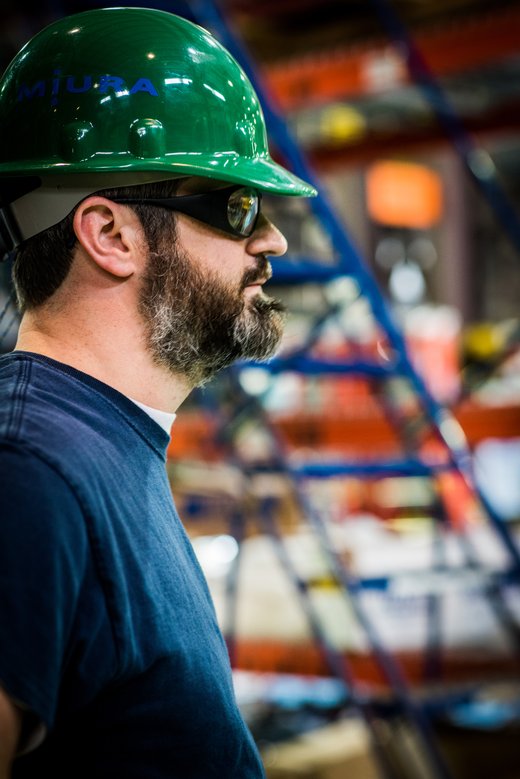
Since those early days of finding a home in Georgia, Miura has become known as one of the best places in the area to go to work. Cody Nichols, the plant’s safety manager, has been there for four years and takes pride in the way the company operates. “This is a great place to work. We know we’re making an innovative product, and it feels good to work for a company that emphasizes quality over quantity,” Cody explains. “The welders and machinists, everyone works their shift, and then picks up the next day, no long hours. It’s another way we put quality over quantity, and make safety the top priority.” That commitment is clear-- Miura is currently one of only 17 factories in Georgia who carry the SHARP certification for safety.
Miura opened in Rockmart, Georgia in 2009 with 20 employees. Now the location holds a team of over 160 welders, machinists, engineers, IT professionals, product developers, support specialists, sales reps, and more. The office staff work alongside one another in a modern, open floor workspace. “It really is a perfect balance of the two cultures. The Japanese believe strongly in collaboration, and that helps support this team environment,” Cody explains.
With the dream of reaching the United States now a reality, Miura shows no signs of slowing down. With a focus on innovative technology and world-class service, “our goal is to just keep growing,” says Mark. “We hold the most market share in Japan, but here in the States we have room to grow. This next generation, will get us to that level.”
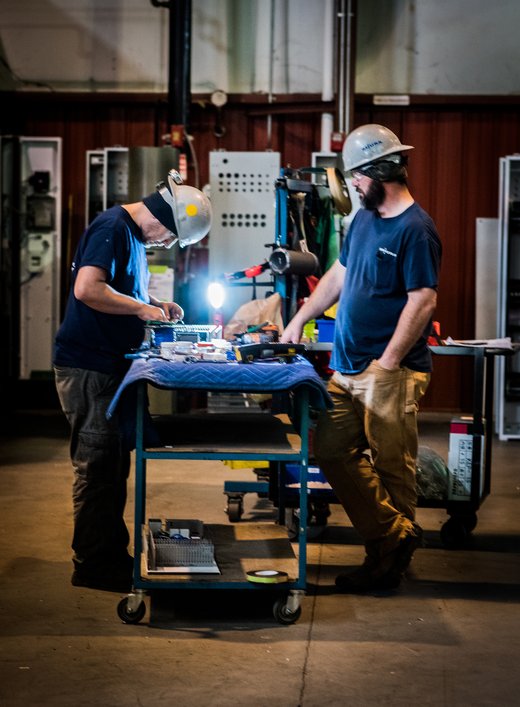
The next generation will certainly have a head start. Miura is supporting a new school for welding, opening in the spring of 2017 in nearby Cedartown. “We have to do some things to help address the workforce issue of robotics and welding in the state,” Mark explains. Students will graduate from the academy highly skilled welders, immediately employable and with training from a real-world setting. For the future of families in Polk county, and for a company started by a dreamer in 1927 Japan, this kind of progress can only be known as kaizen.
DIRTT
Sep 27, 2017